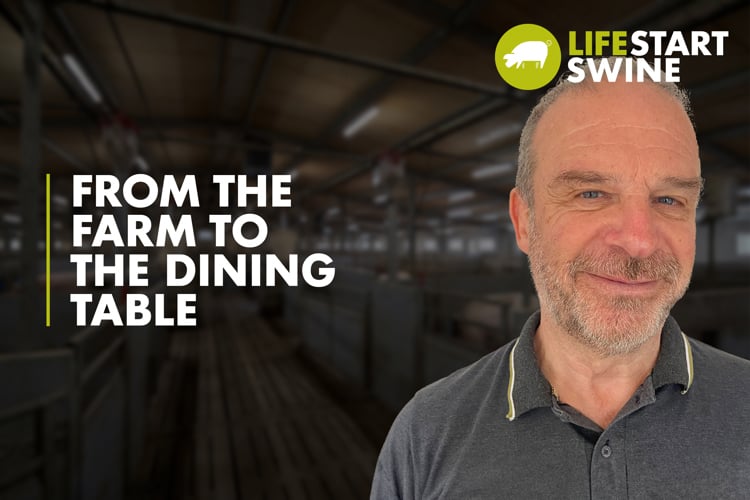
- 2023
- COMMUNITY STORIES
By Roger Campbell, Managing Director RG Campbell Advisory
I’m going to tell you how I was able to get production people interested in research. As you might expect, there needs to be something in it for them.
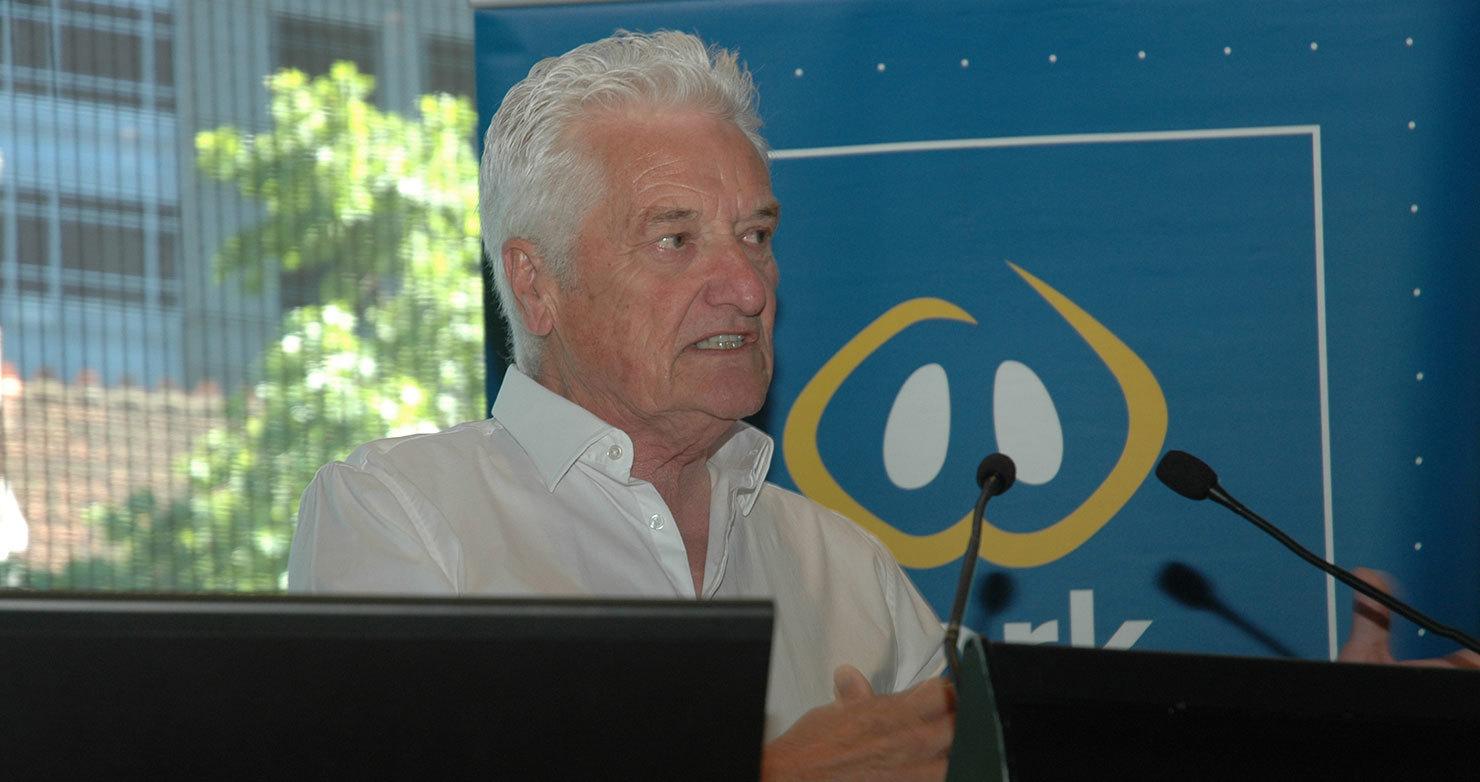
In 1988, after believing I knew everything important there was about swine nutrition, I left my career as a full-time scientist and joined Bunge Meat Industries (now, Rivalea Australia), at the time, Australia’s largest producer of pigs and pork. The business was integrated from feed milling to processing and owned some 30,000 sows. I was based at their largest production site in Corowa, NSW, which had five farrow-to-finish modules (2,000 - 5,000 sows) and a slaughterhouse on site.
I went there on a problem-solving mission but, in 1989, they made me the general manager of technical services. This covered R&D, nutrition, reproduction, animal health, eating quality, and whatever else they thought might be technical. I started with a small team and limited facilities, but jumped into the task with enthusiasm and spent most of 1989 and 1990 working in the barns to sort out what exactly the pigs were doing, where we sat with crucial KPIs, and start setting some targets for improvement.
Production managers and staff were somewhat sceptical, and some staff even made snide comments when I and my right-hand man at the time (Wayne Morley) were in the pens weighing and tagging pigs. We always had pointed but respectful replies, but got the feeling they wanted more than banter.
Eventually, the technical team grew, the company built great research facilities, and we started turning out some interesting and very relevant results. I made certain that the results and their implications were communicated to production managers and their staff, and we established a regular research-production results meeting where we presented what we thought were results that could improve the efficiency or reduce the cost of production.
The general manager of production at the time (Paul Pattison) would consider these results and, if he thought they might have value, would implement them at one or more modules and monitor what changed. If the results were positive, the technology or new idea would be implemented across all production but not always at 100% of what the research data suggested. For example, we showed that the lysine content of the finisher diets could be reduced by 15% without affecting performance. Paul implemented diets with lysine and other amino acids reduced by 10% because he could not afford to adversely affect his budgeted sales numbers or weights.
I also started a monthly R&D report, which went to all modules, so everyone knew what was happening and where it was happening. The module managers and their staff saw production improve and began asking if we could do the next study on their module because, if an idea worked, the module where the work was done was first to get any advantage. Production managers and their staff now saw the technical team as part of the business in general and assisting with projects and/or awaiting the results of projects gave them something to get excited about. They became more curious and wanted to know how we might be able to address something they were having problems with. Most often, all that was needed was a visit to the site and a discussion with the staff. But you always needed to tell them something would be done about it. And then, tell them what and when it was done.
They did develop a researcher mentality. I think it added some excitement to their roles but, like I said, there needed to be something in it for them. It took good communication, being seen on site, and understanding how technology and production intertwined to impact profit. In that way, swine producers and people in the field can become scientists. People will always see the benefits of research if they see how, it can help them in their daily routine.